Manufaktura sektorea industria dinamikoenen artean dago. Gaur egun, etengabeko bultzada dago zehaztasun eta doitasun orokorra hobetzeko, eta hari bidezko elektroerosioa bezalako prozesuak zehaztasun osoz eskaintzen diren prozesuak hobetzeko, eta horiek industriarentzat eraldatzaileak dira.
Beraz, zer da zehazki Wire EDM, eta zergatik hartzen da fabrikazio sektorearentzat iraultzailetzat? Hurrengo testuak fabrikazio teknika sofistikatu honen oinarriak aztertuko ditu, hainbat industriatan aplikazioak dituena.
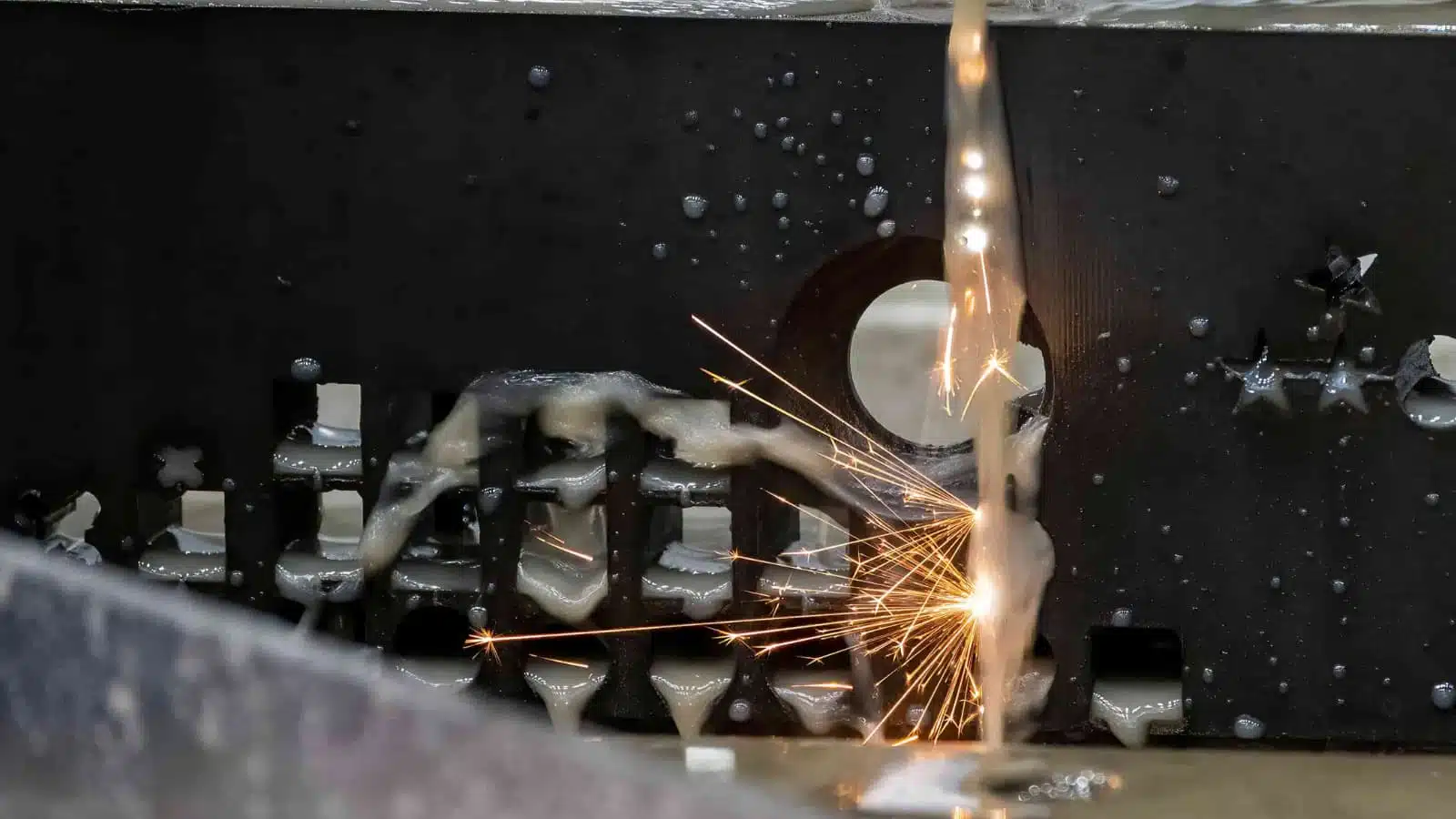
Hari-elektrizitatearen sarrera laburra
Hari bidezko deskarga elektrikoaren mekanizazioa (EDM) 1940ko hamarkadan aitzindari izan zen bi zientzialari sobietarrek, metala deskarga elektrikoarekin higatu zutenek lehen aldiz. Teknologiak aurrerapen nabarmenak izan zituen 60ko eta 80ko hamarkadetan, eta fabrikazioan gero eta ohikoagoa bihurtu zen. 90eko hamarkadaren amaieran, IT eta CNC hobekuntzekin, hari bidezko EDM makinak informatizatuagoak bihurtu ziren, eta horrek haien eraginkortasuna eta zehaztasuna handitu zituen.
Gaur egun, hari-elektrohigadura ezinbestekoa da aeroespaziala, automobilgintza eta medikuntza bezalako industrietan, mekanizazio-metodo tradizionalek paregabeko diseinu korapilatsuak eta forma konplexuak eskaintzeagatik ezaguna.
Harizko elektrohigadura prozesua
Hari bidezko deskarga elektrikoaren mekanizazioa (EDM) metodo zehatz bat da, txinparta elektriko kontrolatuak erabiltzen dituena pieza baten zati txikiak urtzeko. Hari elektrodoak, normalean letoiz edo zinkez estalitako materialez egina, txinparta hori sortzen du eta aurrez ezarritako bide batean mugitzen da. Bere abantaila? Kontaktu fisikorik gabe funtzionatzen du, piezan zein erremintan kalteak edo markak saihestuz.
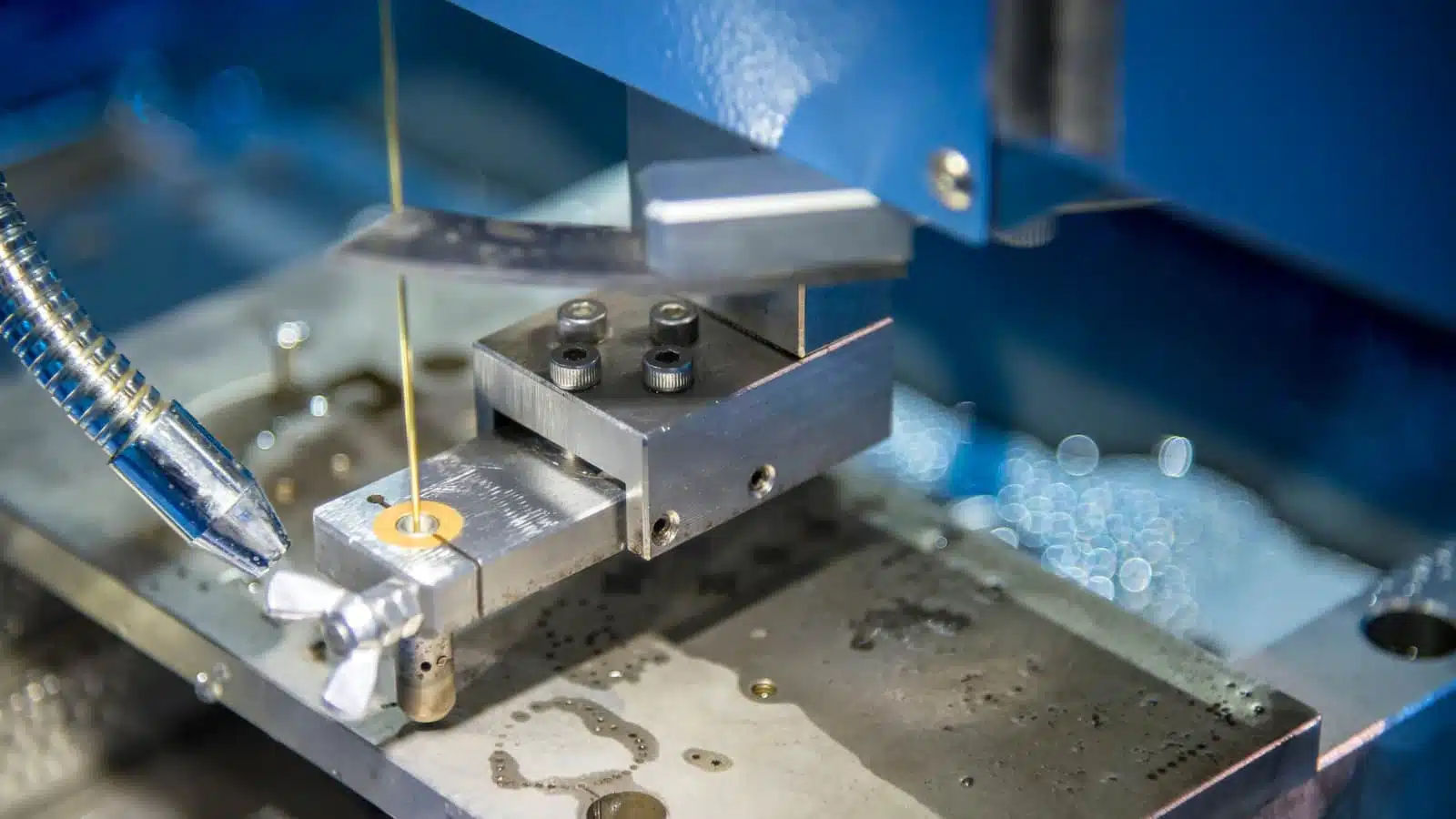
Nola funtzionatzen duen EDM-k
EDM deskarga elektrikoaren energia termikoan oinarritzen da. Deskarga honek pieza urtze-punturaino berotzen du, plasma-kanal txiki-txikiak sortuz. Kanal hauek, askotan mikrometroko tamainakoak, azkar desager daitezke.
EDM prozesua ingurune dielektriko batean gertatzen da, normalean ur desionizatuan. Fluido honek pieza hozten du eta lurrundutako materiala kentzen du, mekanizazio jarraitua erraztuz.
Hari-elektrodoaren garrantzia
Ebakitzaile eta eroale gisa jarduten duenez, alanbre elektrodoa ezinbestekoa da. Letoia edo zinka bezalako materialekin estalita, tenperatura altuetan erreakzioei aurre egiten die. Ordenagailu batek kontrolatuta, ebaki zehatzak bermatzen ditu distortsio minimoarekin eta zehaztasun handiarekin.
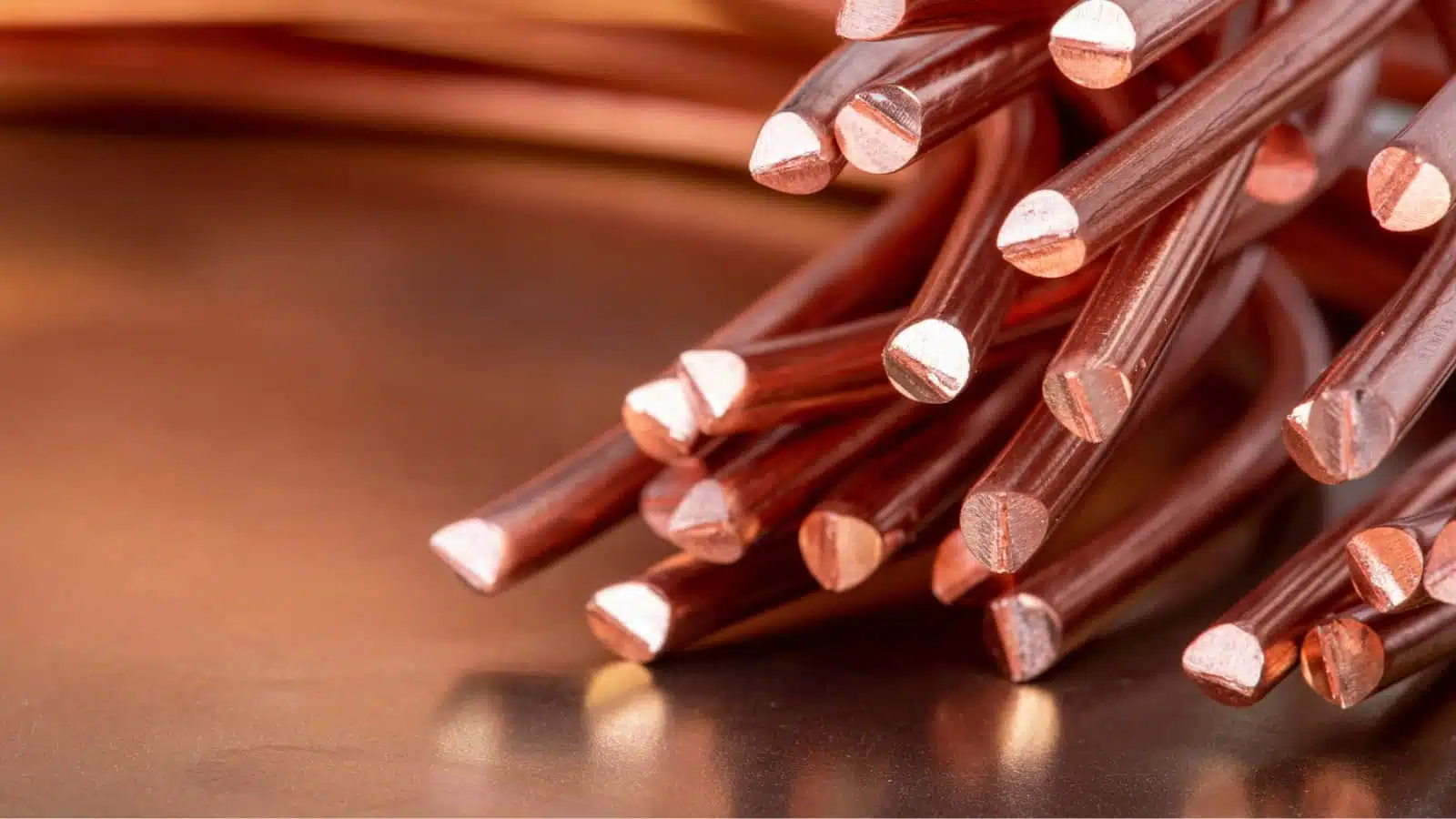
Hari bidezko elektrohigadurarako tolerantziak
Alanbre bidezko ebaketa dauden fabrikazio-prozesu zehatzenen artean dago. Beraz, tolerantzia estuak ez dira ezohikoak horretarako. Benetako tolerantzia hainbat faktoreren araberakoa da, besteak beste, proiektuaren konplexutasunak, mekanizazio-gaitasunak eta operadorearen trebetasunak.
Hala ere, tolerantzia estandarrak eta onargarriak fabrikatzaile askok jarraitzen dituzten industria-erreferentziak dira.
Tolerantzia estandarra eta tolerantzia fina
Tolerantzia estandarra
Tolerantzia linealak: Normalean ±0,005 eta ±0,001 hazbete artekoak dira (0,127 eta 0,0254 mm artean), zuloak, zirrikituak edo profilak bezalako ezaugarrietarako desbideratze onargarria adieraziz.
Zuloen diametroaren tolerantziak: Normalean ±0,0005 eta ±0,001 hazbete artean (0,0127 eta 0,0254 mm), mekanizatutako zuloak definitutako diametroaren barruan mantentzen direla ziurtatuz.
Tolerantzia Fina
Tolerantzia linealak: Mikra mailako zehaztasuna lortzen du, normalean ±0,0002 eta ±0,0001 hazbete artekoa (0,0051 eta 0,00254 mm artean), zehaztasun handiena behar duten aplikazioetarako ezinbestekoa.
Zuloen diametroaren tolerantziak: ±0,0001 eta ±0,00005 hazbete artekoak (0,00254 eta 0,00127 mm artean), hari-elektrizitatearen zehaztasun apartekoa nabarmenduz.
Hari bidezko elektrohigaduran tolerantzian eragina duten faktoreak
Hari-elektrizitatea bere mikra mailako zehaztasunagatik da famatua, aplikazio konplexuetarako aproposa bihurtuz. Hala ere, bere zehaztasuna ez da finkoa eta hainbat faktoreren araberakoa da:
• Makinaren egonkortasuna: Makina egonkor batek ebaketa-ekintzetan zehaztasun hobea bermatzen du.
• Alanbrearen kalitatea eta diametroa: Bere purutasunak, diametroak eta ezaugarri elektrikoek eragina dute mekanizazio-prozesuan. Emaitza optimoak lortzeko, alanbrearen kalitatearen eta diametroaren arteko oreka behar da.
• Lan-piezaren materiala: Material batzuk makinentzat eskuragarriagoak diren arren, materialaren aukeraketa aplikazioaren beharretara egokitu behar da.
• Baldintza garbiak: Dielektriko medioaren fluxua mekanizazio prozesuaren kalitatean eragiten du, materiala kentzen, deskarga elektriko koherenteak egiten eta beroa modu eraginkorrean xahutzen laguntzen du.
• Makinaren Kalibrazioa eta Mantentze-lanak: Makinaren gaitasunak funtsezkoak dira. Operadore trebeak dituzten makina bikainak ezinbestekoak dira tolerantzia onenak lortzeko.
•Egonkortasun termikoa: Hari bidezko elektroerosioaren zehaztasun ezaguna mantentzeko, arku elektriko kontrolatuak ezinbestekoak dira. Ezegonkortasun termikoek zehaztasuna arriskuan jar dezakete, baldintza koherenteen garrantzia azpimarratuz.
Alanbrea mozteko material egokienak
Burdin metalak
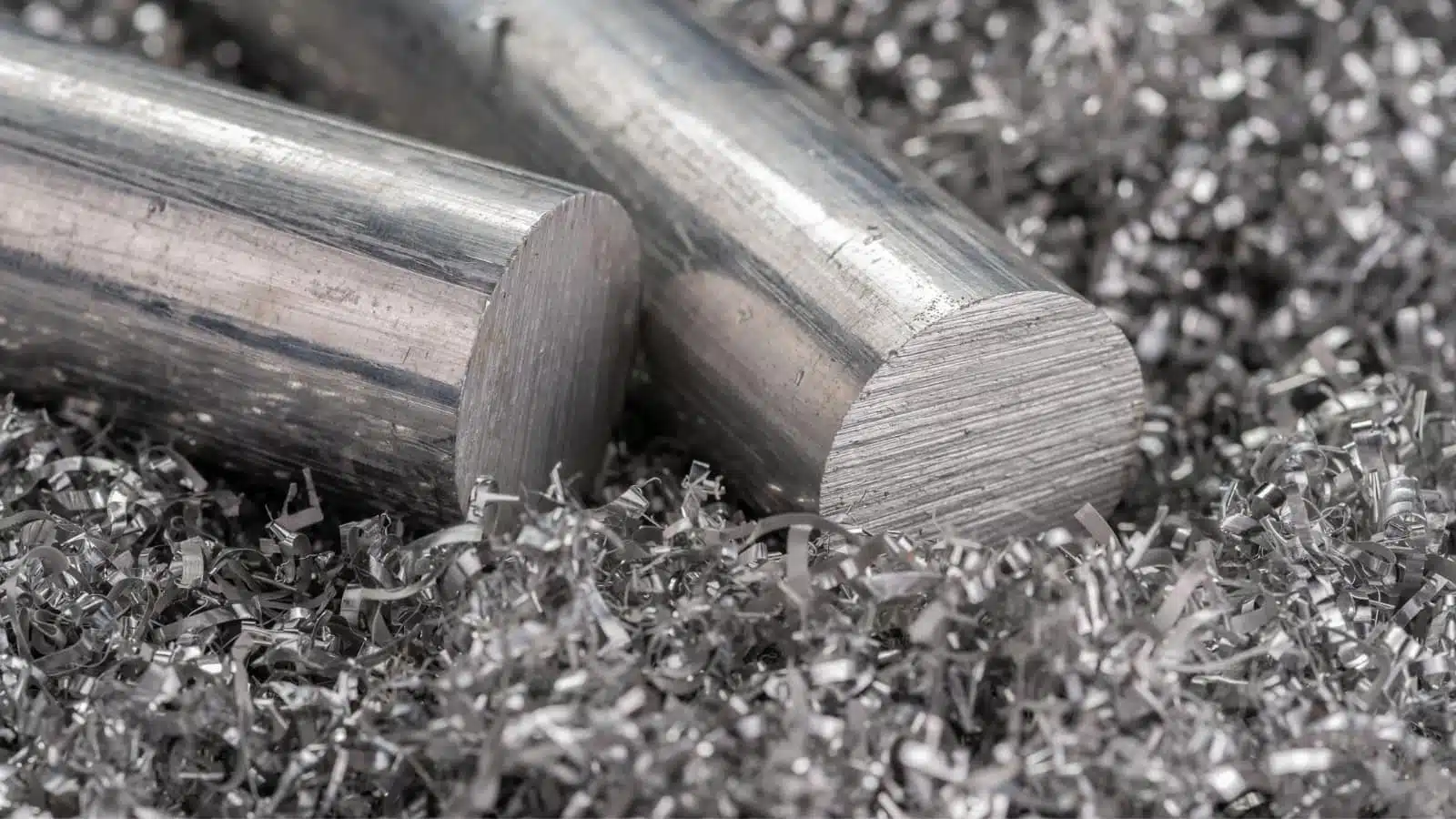
Altzairu herdoilgaitza
Iraunkortasuna eta eroankortasun elektriko bikaina uztartzen ditu. Korrosioari aurre egiteko duen gaitasunak hainbat industriatan material preziatu bihurtzen du. Mekanizazioaren testuinguruan, diseinu zehatz eta xehatuekin duen bateragarritasuna nabarmentzen da.
Tresna-altzairua
Bere gogortze-ezaugarriengatik ezaguna, erreminta-altzairua tresna astun eta zehaztasun-pieza askoren bizkarrezurra da. Berezko gogortasunak, bere propietate elektrikoekin batera, xehetasun korapilatsuetarako eta zorroztasun iraunkorra lortzeko hautagai bikaina bihurtzen du.
Karbono altzairua
Metalen arloan jokalari polifazetikoa den altzairu karbonatua, beste parekoak baino mekanizagarriagoa den arren, perfekziora egokitu daiteke elektrodo eta funtzionamendu-parametro egokiekin. Bere prezio merkeak eta errendimenduak funtsezko elementu bihurtzen dute industria askotan.
Aleaziozko altzairua
Elementuen nahasketa bat izanik, altzairu aleatuaren errendimendua bere osagaien tapiz bat da. Bere nahasketa bereziaren arabera, erresistentzia, iraunkortasuna eta mekanizagarritasuna eskain ditzake, aplikazio askotarako aukera dinamikoa bihurtuz.
Metal ez-ferritsuak
Titanioa
Askotan "espazio-aroaren metala" deitzen zaio titanioaren sendotasunak eta urtze-puntu altuak erronkak sortzen dituzte mekanizazio konbentzionalean. Hala ere, zehaztasun-tresnekin zizelkatuta, diseinu konplexu eta erresistenteak agerian uzten ditu, eta horrek gogokoena bihurtzen du industria aeroespazialean eta medikuntzan.
Aluminioa
Metal arinen artean kuttuna, aluminioa bere eroankortasun elektriko eta xaflagarritasun bikainagatik da ospetsua. Mekanizatzeko erraztasuna eskaintzeaz gain, pisurik gabeko erresistentzia ere agintzen du, garraiotik hasi eta ontziratzerainoko industrietan funtsezkoa bihurtuz.
Kobrea
Eroale bikainena, kobrea mirari elektriko eta elektroniko askoren bihotzean dago. Bere kolore gorrixka-laranja naturalak, osagai xehatuetan moldatzeko duen gaitasunarekin batera, ezinbestekoa bihurtzen du elektronikatik hasi eta arte apaingarrietaraino denetan.
Letoia eta brontzea
Aleazio hauek, urre koloreko tonuetan distiratsuak, ez dira estetika kontua bakarrik. Beren propietate elektriko txalogarriek zehaztasuna edertasunaz bat egiten duten osagaietarako material aproposa bihurtzen dituzte, hala nola bitxi apainduetan edo fin-fin egindako pieza elektronikoetan.
Hari-erosioaren aplikazio nagusiak ingeniaritza modernoan
Hari bidezko elektrohigadura mekanizazioa gero eta indartsuagoa da hainbat material maneiatzeko duen moldakortasunagatik eta xehetasun zehatzak eta tolerantzia estuak lortzeko duen gaitasunagatik, eta horrek funtsezko bihurtzen du fabrikazio modernoan. Hona hemen hiru aplikazio nagusi:
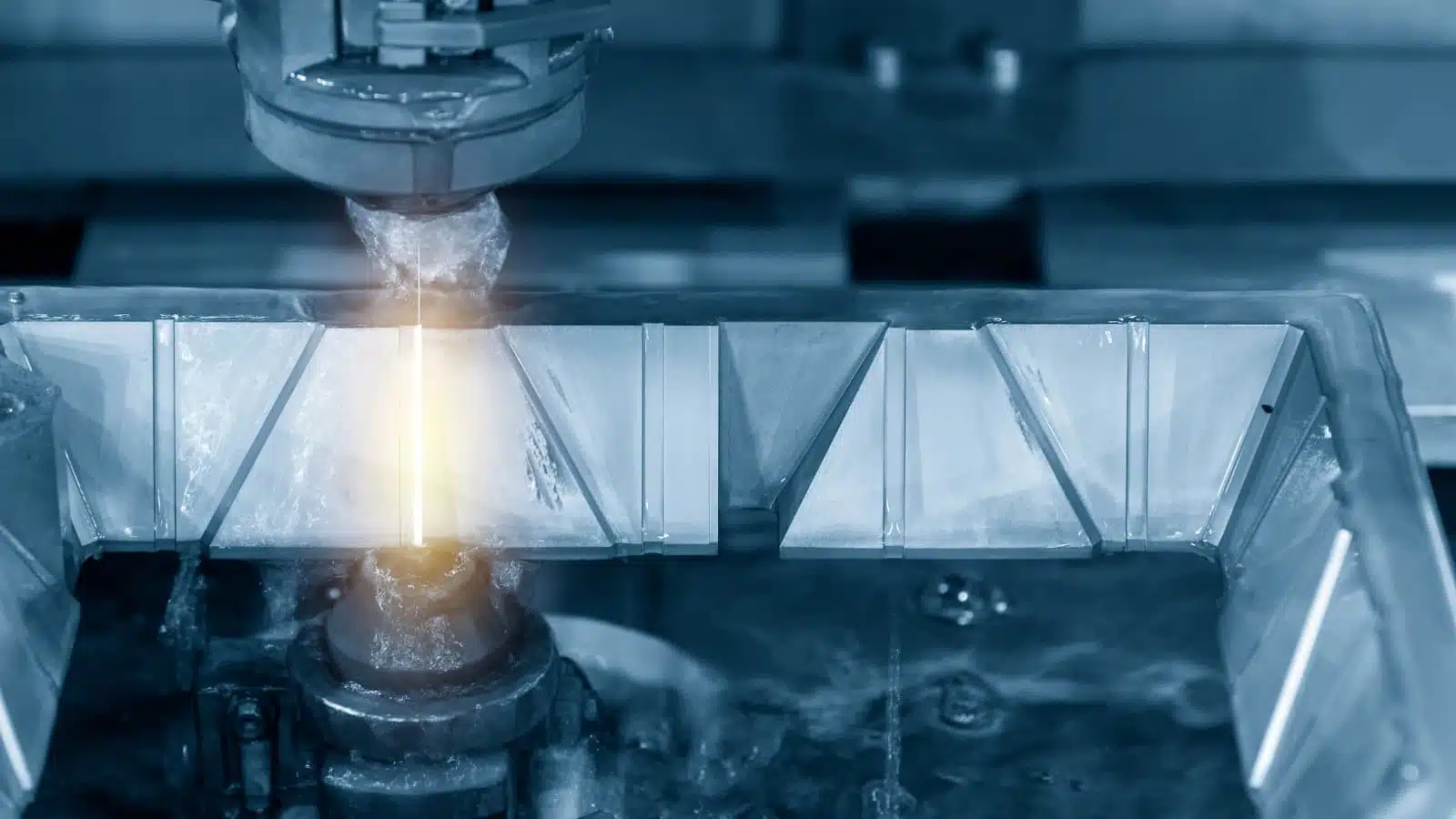
Zehaztasun Piezen Fabrikazioa
Tolerantzia estuekin zehaztasun handiko piezak fabrikatzeko aukera ohikoena. Forma konplexuak, xehetasun finak eta hainbat materialetan ezaugarri txikiak ekoizteko bikaina da.
Aireontzien, medikuntzaren, automobilgintzaren eta elektronikaren industriak hari-elektroerosioaren mende daude engranajeak, toberak, konektoreak eta molde korapilatsuak bezalako osagai kritikoak sortzeko.
Tresna eta trokelen ekoizpena
Hari bidezko elektroerosioa funtsezkoa da forjatzeko moldeak, trokelak eta tresneria espezializatuak egiteko, injekzio-moldeaketatik hasi eta estanpaziorainoko prozesuak barne hartzen ditu. Metodoak neurri zehatzak mantentzeko eta angelu zorrotzak zizelkatzeko duen trebetasunak kalitate gorena eta uniformetasuna bermatzen ditu eskala handiko ekoizpenean.
Prototipoen garapena
Prototipoak azkar eta zehatz egiteko, ingeniariek eta berritzaileek hari bidezko elektroerosioa erabiltzen dute. Horrek diseinuaren baliozkotzea eta proba-fase zorrotzak bizkortzen ditu.
Hari-elektrizitatea erabiliz landutako prototipoek azken produktua islatzen dute zehatz-mehatz, eta horrek produktuaren bilakaera-zikloan duen garrantzia indartzen du.
Arlo nagusi hauetan dituen indarguneak kontuan hartuta, Wire EDM-ren gaitasun zehatz eta zehatzak industria askotan erabiltzen dira.
• Gailu Medikoen Fabrikazioa
• Elektronika eta mikroosagaiak
• Aeroespaziala eta Abiazioa
• Bitxigintza eta Erlojugintza
•Automobilgintza Industria
•Energia Sektorea
• Molde eta trokelen konponketa
Argitaratze data: 2023ko abenduaren 12a